The Vicenza-based company has been working for over 40 years pursuing innovation, process and product technology. Collaborating in contexts characterized by the high complexity as the pharmaceutical sector, the Technical Department of Ecor International has designed and built a new filling tank, designed to provide the highest level of reliability in productive areas where hygienic safety plays a key role. The skills acquired in the field of special welding and materials allow us to meet the needs of the sector by providing tailor-made products.
The context of use
The tank realized by Ecor International team of is conceived for the lines of production of the pharmaceutical world with particular reference to the phase of filling of the drugs usually in liquid form. In particular, the tank, once integrated into a complex system, has the function of collecting the product inside and keeping it in complete safety from external agents. Then, the drug inside the tank waits for the filling line to be ready to receive it so that it can complete the process.
Our filling tanks have been used on many occasions during the production process of Anti-covid 19 vaccines.
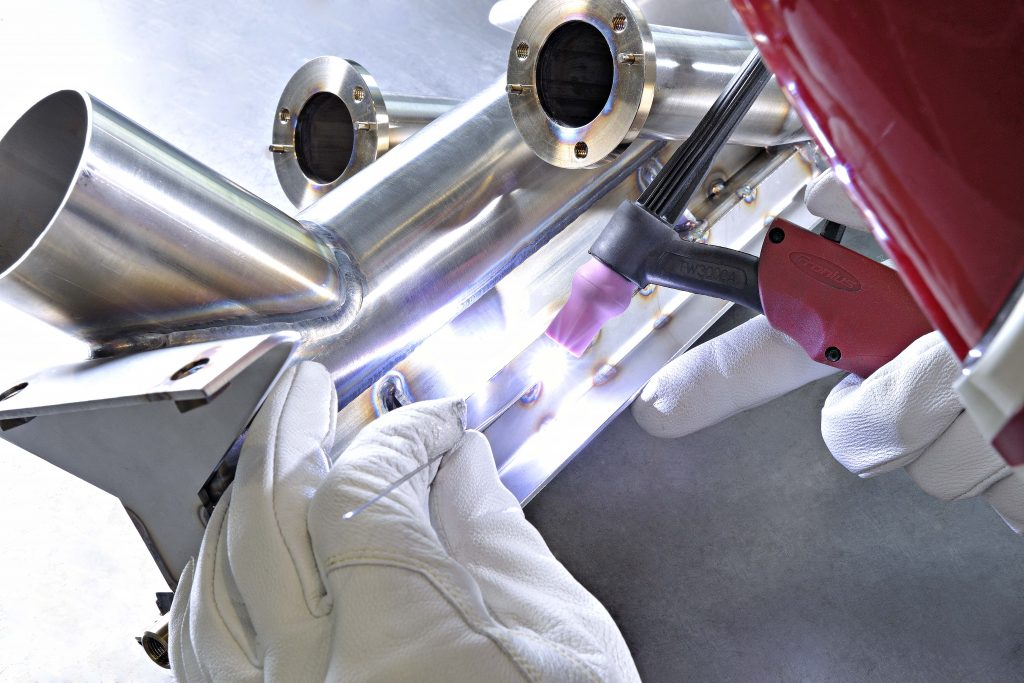
Technical characteristics and controls
To produce the filling tank, the company typically uses AISI 316 L stainless steel – 1.4404 or, for some specific applications, 1.4435 and other special alloys. Starting from the construction of the component by mechanical machining and deformation of the sheet metal, the pieces are welded together using TIG or Laser technology and then mirror polished. This phase allows to obtain very low levels of roughness (below 0.51 Ra – but also 0.1 Ra can be reached) that increase the overall quality and cleanability. Once the production phase is completed – it is carried out internally from the beginning to the end of the process to guarantee safety and control – we test the tanks produced with X-rays, penetrating liquids, cleaning tests with Riboflavin and pressure tests with water and air. In addition, we comply with stringent regulations such as the PED (Pressure Equipment Directive) for the international safety of pressure tanks or the ASME BPE to certify the welding and construction of components for the biopharmaceutical world.
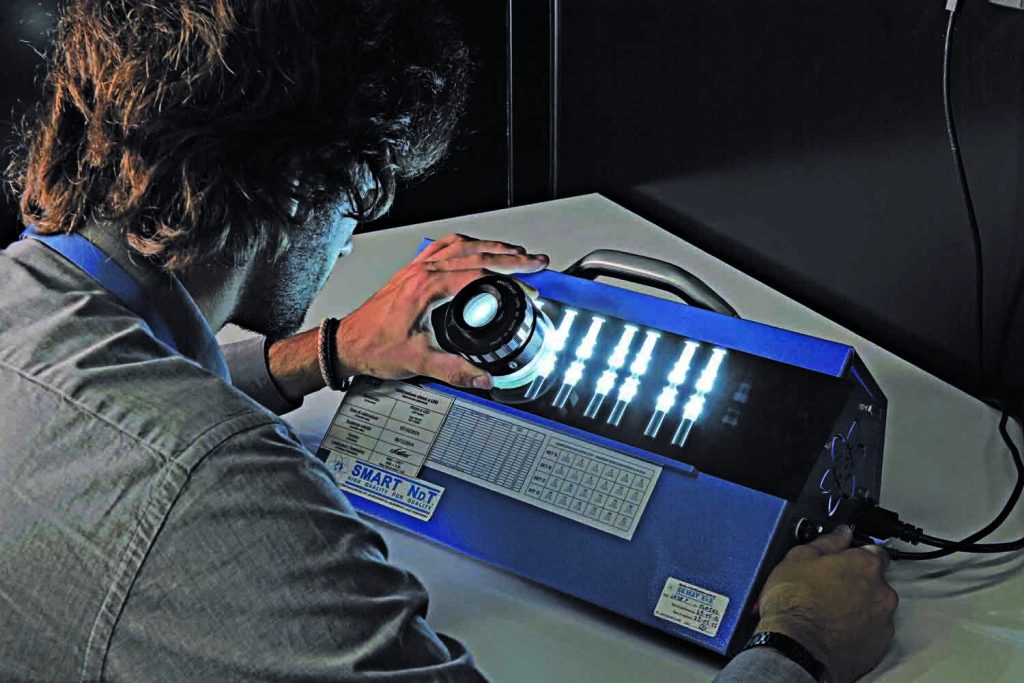